WHAT IS HARD CHROME PLATING?
Well known for its luster and resistance to corrosion, chrome plating is a fascinating process that gives objects a shiny and durable finish.
In this article, we’ll dive into the intricacies of this coating technique, exploring how it works, its applications, and its benefits.
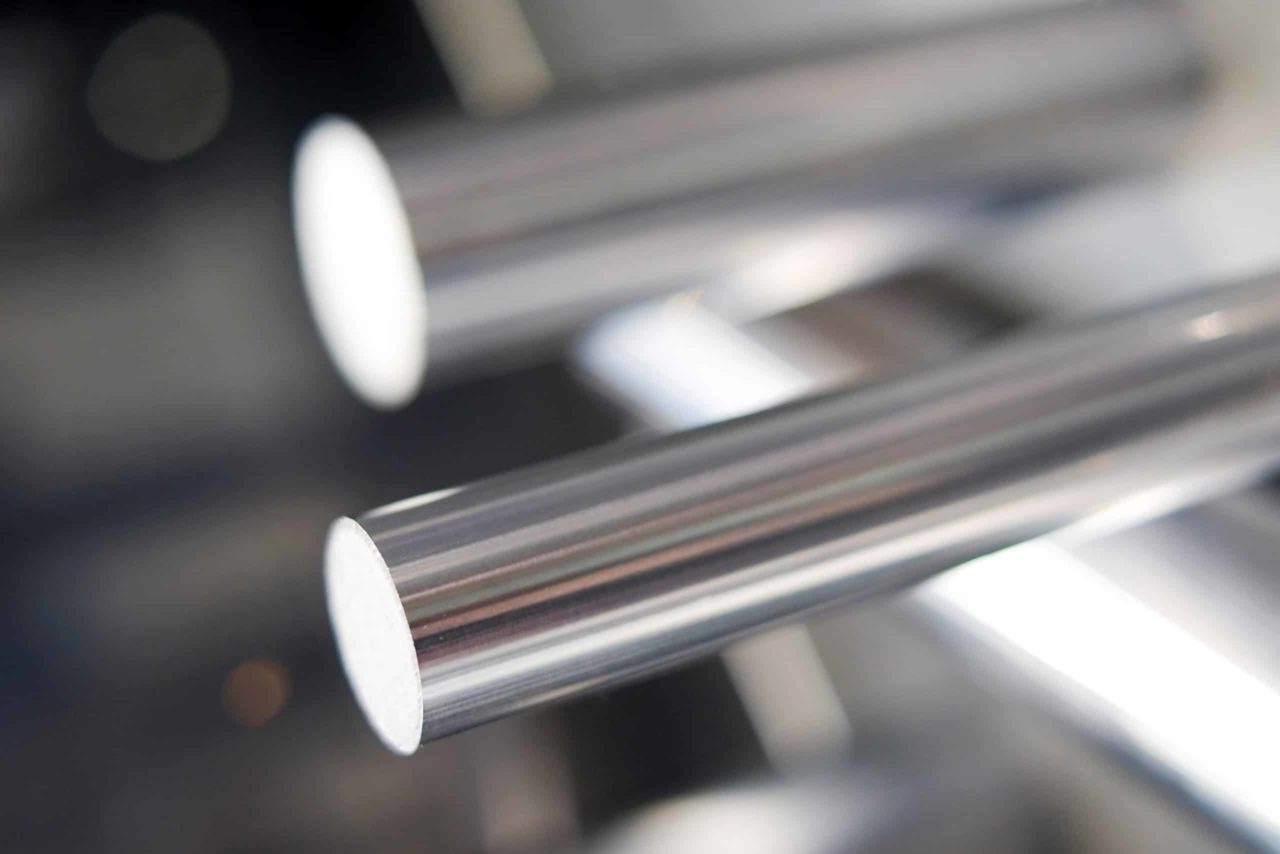
Chrome plating
Hard chrome plating is the process of applying a layer of chrome to a substrate to improve wear resistance, hardness and other surface properties. The term “hard” refers to the high level of hardness (typically 65-70 HRC) and wear resistance imparted to the substrate by the chromium layer. Hard chrome plating is typically applied to metal substrates, such as steel or aluminum, using an electroplating process. The substrate is placed in an electrolytic bath and an electric current is applied, causing chromium ions in the bath to deposit on the surface of the substrate. The thickness of the chromium layer can be controlled by adjusting the electric current and the time the substrate remains in the bath.
The process
Chromium electroplating, also known as electrolytic chrome plating, is an electrochemical plating process that deposits a thin layer of chromium onto a metal surface. In general, the process includes the following steps:
- Preparation of the part: First, the part to be plated is prepared by removing impurities, greases, and contaminants from its surface. This may involve cleaning with degreasers, solvents or specific chemical treatments.
- Pickling: If the part has a layer of previously plated chrome or other coatings, it may require a pickling step to remove these layers. This can be achieved by appropriate chemical baths.
- Activation: The part surface is usually activated to promote adhesion of the chrome plating. This can be done through chemical treatment or immersion in a specific bath to prepare the receptive surface.
- Plating: Once the part is prepared, it is immersed in a plating bath containing a solution of chromium ions. A chrome anode is also placed in the bath. When an electric current is applied, chromium ions are deposited on the surface of the part, forming a uniform chromium layer.
- Finishing: After plating, the part may undergo additional operations to improve the appearance, resistance, and durability of the coating. This may include steps such as polishing, grinding or other specific finishing treatments. Inspection and quality control: Finally, the chrome-plated part is inspected to verify the uniformity of the coating, the absence of defects or imperfections.
- Quality control tests can be carried out to ensure that coating properties, such as hardness and adhesion, meet the required specifications.
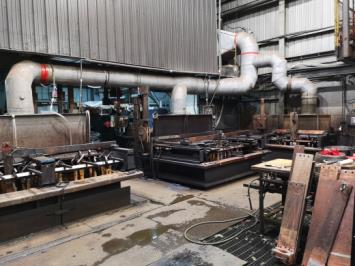
Applications
Thick, hard chrome coatings applied to metal surfaces to improve their resistance to wear, corrosion and other environmental factors. Here are some of the main applications of hard chrome:
- Automotive Industry: Hard chrome is used in the automotive industry for various applications, such as engine parts, drive shafts, brake cylinders, pistons, valves, connecting rods and camshafts. Hard chrome provides excellent wear resistance, reduces friction and improves the durability of automotive components.
- Hydraulic equipment: Hydraulic cylinders, ram rods and hydraulic valves are often coated with hard chrome. This reduces wear from repetitive motion, improves sealing and extends the life of hydraulic equipment.
- Tools and dies: Cutting tools, such as drill bits, countersinks, saw blades and dies, are frequently coated with hard chrome to improve their wear resistance and extend their life. The hard chrome coating reduces sticking of materials to tools, improves thermal conductivity and facilitates the release of dies.
- Industrial Equipment: Hard chrome is used in a variety of industrial equipment, such as shafts, rollers, axles and parts subject to severe wear conditions. The hard chrome coating increases resistance to corrosion and wear, thus extending the durability of the components.
- Chemical Processing Equipment: Vessels, vessels, agitators and components of chemical processing equipment are often hard chrome coated to resist chemical attack and corrosion from aggressive substances found in chemical processes.
Advantages
Hard chrome coatings offer several important advantages, which explains their widespread use in many industrial fields. Here are some of the main benefits of hard chrome coatings:
- Wear Resistance: Hard chrome has exceptional hardness, making it an extremely wear resistant coating. It can withstand high friction, loads and abrasive conditions without rapidly deteriorating, thus extending the life of coated components.
- Corrosion Resistance: Hard chrome offers excellent corrosion resistance, making it suitable for harsh environments, such as those containing chemicals, moisture, or corrosive agents. Hard chrome coating protects metal parts against corrosion and rust formation.
- Aesthetic finish: Hard chrome coatings provide a smooth, shiny and attractive finish. They can be used for decorative purposes, adding a high-end aesthetic to automotive parts, sanitary fixtures, household items, and more. Hard chrome is also easy to clean and maintain, maintaining its shiny appearance for a long time.
- Heat Resistance: Hard chrome is able to withstand high temperatures, making it an ideal choice for applications subject to severe thermal conditions. It retains its mechanical properties and wear resistance even in high temperature environments.
- Low Coefficient of Friction: Hard chrome coatings reduce the coefficient of friction between surfaces, improving movement efficiency and reducing frictional forces. This can lead to a reduction in wear, heating and wear of the components in contact. Retention of dimensions: Hard chrome, thanks to its low thickness and its properties of adhesion, only changes the dimensions of the coated parts very little. This means that precise component tolerances and fits can be maintained after the coating process.
Conclusion
In conclusion, hard chrome is a valuable coating that offers many advantages and finds diverse applications in different industrial sectors. Due to its exceptional hardness, it exhibits remarkable wear resistance, which extends component life and reduces replacement costs. In addition, its corrosion resistance makes it ideal for aggressive environments, effectively protecting metal surfaces from deterioration due to rust and corrosive agents.
CONTACT INFORMATION
2735 Rue Jules Vachon
Trois-Rivières (QC) G9A 5E1
T : 1-877-807-2739